3D 프린팅 산업은 지난 10여 년간 괄목할만한 성장을 했다. 특히 산업용 3D 프린팅 산업은 4차 산업혁명의 핵심 산업으로 주목받고 있으며, 세계 시장 규모도 빠르게 커지고 있다. 이런 산업용 3D 프린팅 기술은 의료, 항공/우주, 자동차 등 다양한 제조 분야에 활발히 적용되고 있으며, 미국과 유럽 등 제조 선진국에서는 제조업 부활을 이끌 수 있는 핵심 기술로 간주하며 투자와 지원을 확대하고 있다.
한국도 산업용 3D 프린팅 기술을 바탕으로 군수 부품 복원, 스마트 금형, 스마트 주조 등 다양한 분야에서 사용이 확대되고 있다. 3D 프린팅 기술은 기존 공장식 제조업에서는 불가능했던 다품종 소량생산을 실현할 수 있어, 기존 생산 방식을 완전히 대체할 수 있는 기술이다.
이런 3D 프린팅 기술의 고도화는 저임금 국가로 이전했던 부품 제조업의 국내 귀환을 가능하게 하여 국내 제조업의 부활을 이끌 수 있을 것으로 평가받고 있다. 이에 정부는 2018년 3D 프린팅 산업 진흥 시행계획을 발표하고 지난해보다 11% 증액된 457억 원을 투입한다고 밝혔다.
3D 프린팅은 산업을 이해하기 위해서는 3D 프린팅 방식을 먼저 알아볼 필요가 있다. 기본적으로 3D 프린팅은 재료를 쌓아 올리는 적층을 통해 제품을 제작하는 방식으로 플라스틱, 금속, 바이오 잉크 등 다양한 재료를 통해 여러 제품을 생산할 수 있다.
3D 프린팅의 다양한 방식
소개할 6가지 3D 프린팅 방식 중 FDM 방식이 가장 대중적이며, DLP와 SLA 방식도 활용 범위가 넓어지고 있다. 이 중 바인더 제팅(Binder Jetting)과 PBF, DED 방식은 금속 재료를 지원해 산업용 3D 프린팅 산업에 적합하다.
① FDM(Fused Deposition Modeling)
FDM는 일반인에게 가장 친숙한 3D 프린팅 방식이다. 가는 실 형태의 필라멘트를 노즐에 서 녹여 한 층씩 적층하며 제작하는 방식이다. 녹아서 적층된 필라멘트는 상온에서 빠르게 식어 그대로 고착되어 형태가 만들어진다. FDM 방식의 3D프린터는 3D프린터 중 가장 저렴하며, 100만 원대 제품부터 구매할 수 있다.
이 FDM 방식에 사용되는 필라멘트는 사탕수수 원료와 옥수수로 만들어진 친환경적인 PLA와 플라스틱 ABS다. PLA는 사포나 조각칼을 이용한 변형이 비교적 수월하여 후가공이 편리하고, ABS는 튼튼한 편이나 후가공이 다소 어려운 편이다.
FDM 방식은 쉽고 빠르게 제작할 수 있어 간단한 시제품 제작에 많이 사용되고 있다.
.jpg)
② DLP(Digital Light Processing)/SLA(Stereo lithography)
DLP와 SLA는 서로 다른 방식이지만 같은 액상 소재인 레진을 경화해 제작하는 방식이다. DLP는 빛, SLA는 레이저를 사용해 레진을 굳힌다. 두 방식은 다른 방식에 비교해 정교하고 표면이 매끈하다는 장점이 있지만, FDM 방식과 비교해서는 제작비용이 더 비싼 편이다. 소형 물체 제작에 적합하며, 산업에서는 치과, 주얼리 등 소량 금속용 소프트 금형 제작에 활용되고 있다.
③ Binder Jetting
바인더 제팅은 현존하는 3D 프린팅 기술 중 가장 다양한 재료를 사용할 가능성을 가진 기술이다. 접착제 적층 기술로 재료와 접착제로 적층을 할 수 있다. 어떤 재료든지 분말로 작게 만들어 적합한 접착제로 잉크젯 프린터처럼 헤드에서 원하는 위치에 접착제를 분사하고 이후 롤러가 기존 재료 또는 원하는 다른 재료로 접착제 위를 덮어 적층한다. 1m 이상의 대형 중자 및 주형을 제작할 수 있다. 일반 주물사를 비롯해 시멘트, 세라믹, 금속 등 다양한 소재를 적층할 수 있다. 산업에서는 대형 구조물용 간접 제조 방식에 활용(주물사 금형 제작)되고 있다.
④ PBF(Powder Bed Fusion)
PBF 방식은 금속 분말에 얇게 깔고 레이저 프린터와 같은 원리로 고출력 레이저를 분말에 조사해 용융시키는 방식으로 형상을 만들어 낸다. DED 방식보다 강도는 떨어지지만 복잡한 형상제작에 유리하며 금속 3D 프린팅 시장에서 널리 사용되고 있다. 현재 산업에서는 터빈블레이드, 베인 등 금속 구조체 생산에 활용된다.
.jpg)
⑤ DED(Direct Energy Deposition)
DED 방식은 고에너지(레이저, 전자빔)원으로 원재료를 녹여 부착하는 방식이다. 금속 제품 제작이 가능하고, 금형 제작 등 여러 산업군에 영향을 미칠 수 있다. 일부에서는 3D 프린팅 기술 중 가장 진보한 기술이라고 부르고 있다. 절삭가공(밀링)과 결합해 하이브리드 3D프린터 제작과 같은 여러 소재나 기술과의 확장이 쉽다. 파우더 분사와 동시에 급속하게 응고하기에 정확하고 미세한 조직을 갖춘 출력물 제작이 가능하다. 큰 치수도 출력할 수 있다. 산업에서는 노후 부품 수리(항공기, 철도) 및 새로운 가공 장비를 만들 때 사용한다.
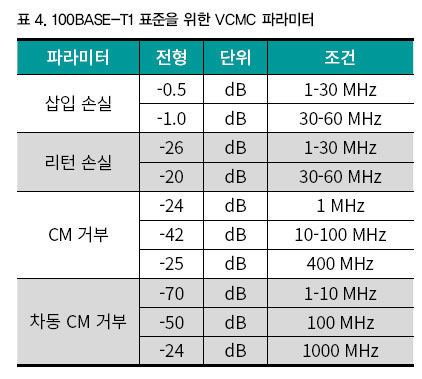
산업용 3D 프린팅의 발전, 무궁무진한 미래
3D 프린팅 산업은 과거 시제품을 만드는데 사용되던 소극적인 활용이 아닌 제품이나 부품을 직접 만들어 사용하는 등 적극적으로 사용되고 있다. 3D 프린팅이 산업에 본격적으로 사용될 준비를 마친 셈이다.
앞서 이야기했듯이 3D 프린팅 기술은 어떤 재료를 사용하느냐에 따라 무궁무진하게 제품을 만들 수 있다. 식용 재료를 사용하면 음식도 만들 수 있고, 시멘트를 재료로 쓰면 건물도 지을 수 있다. 이런 다양한 재료 중 가장 주목을 받는 것이 바로 금속 재료다. 금속 3D 프린팅(메탈 3D 프린팅)은 제조업에서의 활용 범위를 크게 늘려주고, 더 많은 기업이 3D 프린팅 기술을 사용할 수 있도록 만들고 있다.
금속 3D 프린팅 기술은 우주 항공(항공기 연료 노즐, 펌프, 브래킷 등), 의료(임플란트, 고관절 등), 금형(제작 및 유지보수), 산업 기계(다품종 소량 생산 부품) 분야에서 사용되고 있다.
항공기의 유압유 저장통 거치대(Hydraulic Reservoir Rack)는 과거 126개 부품과 27개 체결장치, 61개 너트로 구성되었던 복잡한 부품이었다. 제작에 총 20일이 소요됐던 것을 금속 3D 프린팅 기술을 통해 1개의 부품으로 간소화했고 제작 기간도 2일로 단축했으며, 중량도 50% 감소했다. 복잡하게 구성되었던 부품이 단순화됐고, 제작시간도 1/10로 감소했다. 금속 3D 프린팅 기술로 만든 부품이 얼마나 효율이 높은지 보여주는 예다.
레이싱 카(Racing Car)에 사용되는 실린더 헤드를 금속 3D 프린팅 기술을 통해 개선한 사례도 있다. 금속 3D 프린팅 기술을 통해 체적이 70% 감소했고, 표면적이 7배 증가해 냉각 효율이 향상됐다. 더불어 진동 및 중량이 감소해 저진동 경량 엔진 실린더 헤드를 만들었다.
1.3m 크기의 거대한 선박용 프로펠러도 금속 3D 프린팅 기술을 통해 제작 효율을 높였다. 6축 로봇암 타입의 3D 프린터를 이용해 제작했는데 기존 공법대비 제작 기간이 몇 주 이상 단축됐다.
자동차의 핵심 부품인 엔진에 들어가는 주요 부품들도 금속 3D 프린팅 기술을 통해 제작함으로써 개선됐다. 르노 트럭에 사용되는 DTI5 4 실린더 엔진에 사용되는 로커암(Rocker arms), 캠축 베어링 캡스(Camshaft bearing caps) 등 부품 수와 중량을 25% 경량화했다.
.jpg)
주목해야 할 해외 기업
① GE(General Electric)
GE는 세계 3D 프린팅 제조 장비 기업 중 가장 규모가 큰 기업으로 적극적으로 3D 프린팅 기술 투자하고 있다. 3D 프린팅을 위한 자회사인 GE어딕티브(GE Additive)를 설립하고, 2020년까지 1조 원 매출이라는 구체적인 목표도 설정했다. 공격적인 인수합병도 진행했다. 지난 2016년 Arcam AB와 SLM Solutions Group AG 등 독일과 스웨덴의 금속기반 3D 프린팅 회사를 1조 5천억 원에 인수했고, 미국 앨라배마주와 사우스캐롤라이나주에 항공기 등에 사용되는 부품을 대량생산하기 위한 공장을 건립하기도 했다.
GE는 2015년 금속 3D 프린팅 기술을 통해 제트기 엔진 부품을 제작했고, 이는 첫 상용화 사례였다. 현재 GE는 연간 10만 개 이상의 3D 프린팅 부품을 항공기 엔진과 발전기 터빈 등에 사용하고 있다. 여기에 3D 프린팅으로 만든 부품이 큰 비중을 차지하는 최초의 상업용 항공기 엔진인 항공기 엔진인 어드밴스드 터보프롭(Advanced Turboprop)을 개발했다. 이를 통해 기존 항공기 엔진의 개별 부품 수를 855개에서 12개로 줄였고, 엔진 부품의 1/3 이상을 3D 프린팅으로 제작하고 있다.
여기에 에어버스(Airbus), 보잉(Boeing), 중국 상용항공기공사(COMAC)의 차세대 단일통로 항공기에 탑재될 LEAP 제트엔진용 연료노즐도 3D 프린팅 기술로 생산 중이다.
② 지멘스(Siemens)
독일의 지멘스도 3D 프린팅 시장에 뛰어들어 상당수를 상용화했다. 지멘스는 세계 최초로 원자력발전소에 들어가는 터빈 블레이드 등 금속 부품을 3D 프린팅 기술로 제작해 상용화에 성공했다.
지멘스는 3D 프린팅 산업을 위해 3D 프린팅 기반의 온라인 부품 제조 플랫폼을 개발 중이다. 올해 중반 공개할 계획으로 커뮤니티 구성원을 연결해 자원 활용도를 극대화하고 사업 기회를 확대해 부품 구매자와 공장이 세계 어디서나 3D 프린팅으로 부품을 생산할 수 있도록 소프트웨어를 지원한다는 계획이다. 지멘스는 에코 시스템을 만들어 산업계에서의 지위를 높인다는 계획이다.
③ 데스크탑 메탈(Desktop Metal)
데스크탑 메탈은 지난 2015년 설립된 3D 프린팅 솔루션 스타트업이다. 본사는 미국 매사추세츠주 벌링턴에 있으며, 3D 프린팅 전문 회사 최초로 시리즈 D 벤처 펀딩으로는 최대 규모인 2억 1200만 달러(약 2,270억 원)에 달하는 자금을 조달했다. 2017년에는 세계경제포럼(WEF)에서 선정하는 세계 30대 기술선구자(Technology Pioneers) 기업 중 하나로 꼽혔고, 최근에는 MIT 테크놀로지 리뷰의 50대 스마트 기업 리스트(50 Smartest Companies)에도 선정됐다.
최근에는 자동차업체 포드가 데스크탑 메탈에 6,500만 달러(약 700억 원)를 투자했다. 데스크탑 메탈의 3D 프린팅 기술은 금속과 세라믹 파우더를 부드러운 폴리머와 결합한 소재를 압출해 쌓는 방식으로 1차 혼합물을 만들고 이후 용광로에 들어가 폴리머는 연소하고 금속과 세라믹 소재 부분만 남아 굳어지는 과정을 거친다. 이를 통해 제조물은 구조적 완성도 면에서 주조한 금속 부품과 비슷하며 별도의 보완 작업이 필요 없다.
.jpg)
한국의 3D 프린팅 기술의 현주소는?
국내 3D 프린팅 산업은 미국, 독일 등 선도국가와 비교하면 아직 규모도 작고, 제품도 시제품에 맞춰져 있다. 그러나 최근에는 제품 양산, 상용화에 3D 프린팅 기술을 사용하고 있으며, 관련 업체들도 늘어나고 있다. 국내 3D 프린팅 산업을 알아보기 위해서는 시장을 이끄는 주요 업체들을 알아볼 필요가 있다. 센트롤과 캐리마, 맥스로텍을 간단히 살펴보자.
① 센트롤
2014년부터 3D 프린팅 사업을 진행한 센트롤은 기존 CNC 분야에서 축적한 기술을 바탕으로 국내 최초의 금속 3D 프린터를 개발했고, 세계 세 번째로 주물사 3D 프린터를 개발했다. 지난해에는 국내 업체로 처음으로 중국에 100억 원 상당의 산업용 3D 프린터를 수출했다. 센트롤은 중국을 비롯한 일본과 인도, 러시아에 3D 프린터를 수출한 바 있다.
현재 독일과 일본의 소재 업체와 3D 프린팅 소재 개발을 공동으로 추진하고 있으며, 금속 3D 프린터를 활용한 사출금형센터도 건립을 준비 중이다. 더불어 울산시에 소재개발 및 양산 체제 구축을 위한 스마트팩토리를 건설할 예정이며, 주조센터 설립도 계획하고 있다.
최근에는 제품 디자인부터 양산까지 모든 공정을 자체 진행하는 ‘센트롤 원스톱’서비스 체제를 구축했다. 이를 통해 3D모델링부터 기구설계, 시제품 제작, 금형 제작, 양산까지 모든 공정을 원스톱 서비스로 받을 수 있고 소요 기간도 1개월 안팎으로 단축할 수 있다.
② 캐리마
캐리마는 지난 2015년부터 3D 프린팅 사업을 진행해 국내 최초 DLP 3D 프린터를 제조했다. 현재 7개 나라에서 대리점을 운영하고 있으며, DLP 3D 프린터인 마스터를 비롯해 주얼리용 3D프린터 IM 시리즈, 산업용 DM시리즈를 일본, 러시아 등 25개국에 수출을 했다.
캐리마는 치과와 주얼리, 산업 분야를 공략하고 있으며, 기존보다 25배 향상된 'C-CAT' 적층 정밀 기술을 통해 차별화를 진행하고 있다. 기존 DLP 방식의 경우 1시간에 2~3cm를 출력했던 것과 비교해 C-CAT 기술은 1시간에 60cm를 출력할 수 있다. 정밀도가 0.02mm로 우수하면서도 표면이 매끄러워 후가공이 필요 없다. 면단위로 조형해 작업 속도가 균일하고 빠르다. C-CAT 소재를 사용하면 되는데 캐리마는 소재부터 소프트웨어까지 최적화해 자금이 확보 되는 대로 양산 체재를 갖출 계획이다. 더불어 의료와 바이오 분야의 사업을 강화할 계획으로 치과 분야에서 널리 사용되고 있으며, 추가로 정형외과 분야에서도 활발히 사용될 수 있도록 노력할 계획이라고 밝혔다.
③ 맥스로텍
코스닥 상장사인 맥스로텍은 2015년부터 금속 3D 프린터 개발에 뛰어들어 독자 기술로 개발에 성공했다. 공작기계와 5축 병렬로봇, 갠트리 로봇(직각으로 움직이는 로봇)으로 기술력을 축적해온 맥스로텍은 3년에 걸친 개발 기간을 걸쳐 지난해 8월 시험 출력에 성공했고, 연말부터 본격적으로 시제품 제작을 의뢰받아 사업을 진행하고 있다. 5축 병렬로봇을 접목한 3D 프린팅 기술은 3개의 직선 운동과 2개의 회전 운동을 통해 제한 없이 제품을 출력할 수 있다. 현재 최대 60cm로 출력할 수 있다. 스테인리스틸, 인코넬(니켈합금), 텅스텐 등 금속 재료를 사용할 수 있다.
올해 6월 갠트리 로봇을 결합해 1m 규모의 출력물이 가능한 금속 3D 프린터 '타입 1‘을 선보일 예정이다. 또 2018년에는 길이 2m, 무게 8톤까지 출력이 가능한 ’타입 2‘ 금속 3D 프린터를 개발할 예정이다. 타입 2에는 축이 3개 더 늘어난 8축 병렬로봇을 결합할 계획이라고 밝혔다.
맥스로텍은 출력 서비스를 본격 진행할 계획으로 먼저 수입에 의존하는 발전설비용 부품을 직접 출력할 계획이다. 발전설비용 부품은 수급에 오랜 시간이 걸리고 작은 부품 파손 때문에 모듈 전체를 바꿔야 하는 경우도 있어 수요가 있다.
.jpg)
.jpg)
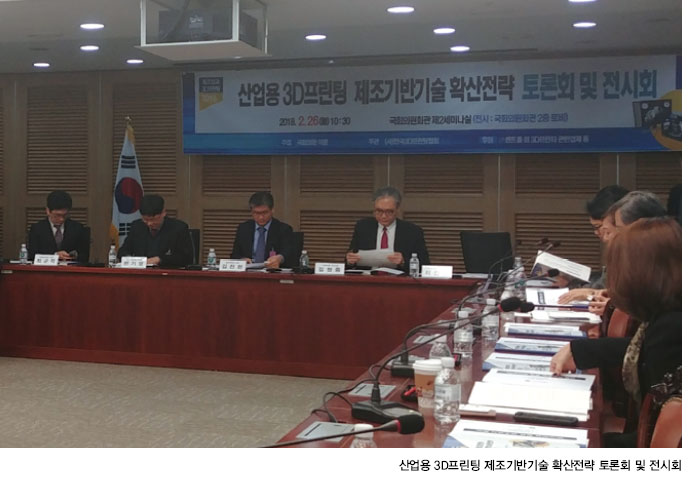
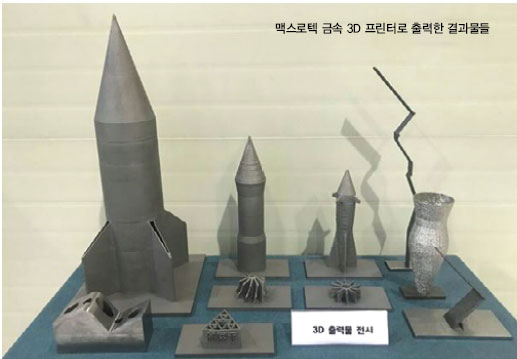
3D 프린팅 산업, 미래를 바꿀 준비 마쳐
3D 프린팅 기술은 기초적인 기술의 준비만 마쳤을 뿐 아직 발전 가능성이 무궁무진하다. 소재를 비롯해 3D 프린팅의 속도와 정교함, 편리함 등 아직 부족한 부분이 있어 꾸준히 개선될 것이다. 더불어 4차 산업혁명과 밀접한 관련을 맺으며 응용 기술로 놀라운 혁신을 가져올 것으로 전망된다.
이런 3D 프린팅 산업은 이제 본격적으로 상용화와 함께 규모의 경제를 이룰 전망이다. 아직 대량 생산보다는 다품종 생산에 좀 더 적합하지만, 충분한 투자가 뒷받침되면 3D 프린팅만으로 기존 제조 설비를 대체하는 효과를 거둘 것이다.
3D 프린팅 산업이 고도화되면 주문과 동시에 생산되어 재고 관리가 필요 없는 새로운 형태가 나타날 것이다. 복잡한 제조 과정도 2~3개 단계만 거치면 바로 양산할 수 있는 빠른 속도를 가질 것이다. 음식도 만들고, 건물도 만드는 놀라운 광경이 일상화될 날이 머지않았다.
걸음마를 뗀 3D 프린팅 산업은 앞으로 뛰다 못해 날아오를 것이다. 3D 프린팅 산업이 가진 잠재력은 무한에 가깝다. 이런 3D 프린팅 산업의 경쟁력을 확보하기 위해서는 정부와 기업이 발 벗고 나서야 한다. 새로운 제조업 환경이 꿈틀대고 있는 지금이 바로 투자와 기술 개발하기 딱 좋은 시기다.
<저작권자©스마트앤컴퍼니. 무단전재-재배포금지>