반도체 산업 확장 견인하는 강력한 트렌드에 맞춰 수익성 높은 성장
“어플라이드 머티어리얼즈(Applied Materials)는 전세계 모든 반도체 칩과 첨단 디스플레이 제품 생산에 사용되는 재료공학 솔루션 분야 선도 기업이다. 원자 단위를 비롯해 산업 전반을 아우르는 재료공학 분야 전문성으로 고객의 가능성을 현실로 구현하고 있다. 미래를 여는 새로운 기술을 개발하는 혁신 기업이다. 한국법인 어플라이드 머티어리얼즈 코리아(Applied Materials Korea)는 최첨단 기술과 글로벌 선진 사례를 국내 공유하고, 국내 기업으로부터 부품을 조달 받으며 한국 IT 산업 발전에 기여해 왔다. 1989년 반도체 장비 분야를 시작으로 디스플레이 장비 분야까지 확장하여 현재까지 활발한 사업을 이어오고 있다.”
박광선 대표이사, 어플라이드 머티어리얼즈 코리아
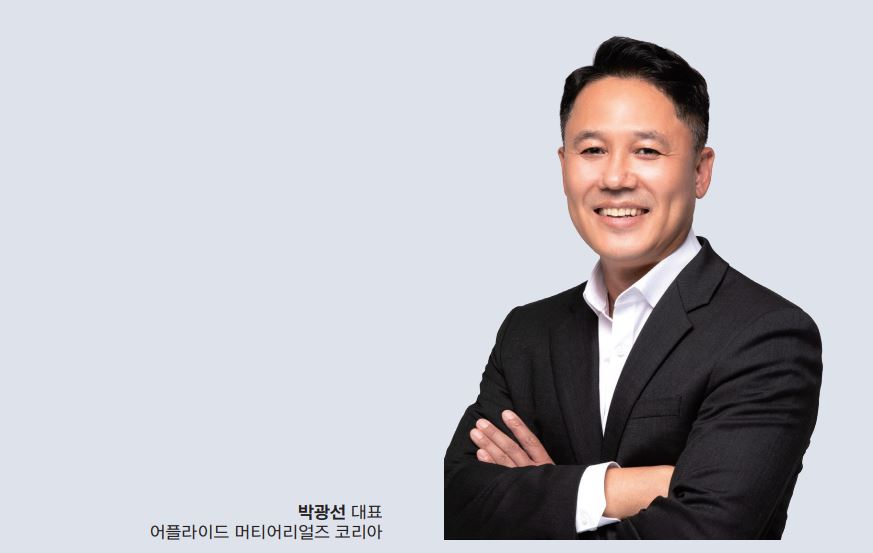
어플라이드 머티어리얼즈는 회계연도 2023년 4분기 67억 2000만 달러의 수익을 창출했다고 밝혔다.
재료공학 솔루션 분야 글로벌 선도 기업 어플라이드 머티어리얼즈가 10월 29일 마감한 회계연도 2023년 4분기 및 전체 실적을 발표했다. 어플라이드 머티어리얼즈 회계연도 2023년 전체 매출은 미국회계기준으로 265억 2000만 달러를 기록했다. 매출총이익률 46.7%, 영업이익과 영업이익률은 76억 5000만 달러와 28.9%, 주당순이익 8.11 달러로 나타났다.
게리 디커슨(Gary Dickerson) 어플라이드 머티어리얼즈 회장 겸 CEO는 “어플라이드는 광범위한 제품 포트폴리오, 강력한 고객과의 관계, 주요 기술 변화에 대한 리더십을 갖췄다. 이를 기반으로 어플라이드는 향후 몇 년 간 반도체 산업 확장을 견인하는 강력한 트렌드에 맞춰 수익성 높은 성장을 거둘 좋은 위치에 자리잡았다”고 밝혔다.
한편, 어플라이드 머티어리얼즈 코리아(대표 박광선)가 글로벌 신뢰경영 평가 기관 GPTW(Great Place to Work Institute) 선정 ‘2023-2024 밀레니얼이 가장 일하기 좋은 기업’을 수상했다.
이번 평가에서 어플라이드 머티어리얼즈 코리아는 밀레니얼 세대(만 19세-만 34세) 기대 사항에 부응하며 ‘2023-2024 밀레니얼이 가장 일하기 좋은 기업’으로 선정됐다. 어플라이드는 지난 9월 GPTW으로부터 ‘2023년 대한민국 일하기 좋은 일터 인증’을 받은 바 있다.
박광선 어플라이드 머티어리얼즈 코리아 대표는 “어플라이드는 혁신을 통해 더 나은 미래를 만든다는 비전 아래 다양한 관점과 배경, 경험을 지닌 구성원이 함께 문제를 해결하고 협업하는 문화를 조성하고 있다”며, “앞으로도 어플라이드는 모든 직원이 소속감을 느끼고, 최고의 역량을 발휘하여 성장할 수 있는 포용적인 문화 형성을 위해 노력할 것”이라고 밝혔다.
2023 Best Product & 2024 Focus Product
1. 지난 10여 년간 가장 중대한 혁신, 웨이퍼 생산 플랫폼 ‘비스타라(Vistara)’
혁신적 트랜지스터, 메모리, 배선 생산…수율 저하 원인 차단해
어플라이드 플랫폼 사상 지난 10여 년간 가장 중대한 혁신을 이룬 비스타라는 반도체 제조사에게 유연성, 인텔리전스, 지속가능성을 제공해 증가하는 반도체 생산 문제 해결을 지원한다. 비스타라는 어플라이드의 하드웨어, 소프트웨어, 공정 기술, 생태효율성 설계 팀 소속 엔지니어 수백 명이 4년 이상 개발한 끝에 완성됐다.
유연성
비스타라 플랫폼은 전례 없이 어플라이드와 파트너사의 다양한 챔버 유형, 크기, 구성과 호환된다. 4개 또는 6개 웨이퍼 배치 로드 포트, 최소 4개에서 최대 12개 프로세스 챔버로 구성돼 다양한 워크로드에 대응 가능하다.
비스타라 플랫폼은 원자층 증착, 화학 기상 증착 공정에 사용되는 소형 챔버는 물론 에피택시, 식각 공정에 쓰이는 대형 챔버와도 호환된다. 어플라이드와 어플라이드 고객은 이 챔버를 결합해 통합 재료 솔루션(IMS) 레시피를 개발할 수 있으며, IMS 레시피를 통해 여러 순차적인 웨이퍼 생산 공정 단계가 진공 상태의 동일한 시스템 내에서 완료된다. 비스타라의 유연성은 이전에는 불가능하던 IMS 기술의 여러 조합을 반도체 제조사에 제공한다. 이에 따라 반도체 제조사는 혁신적 트랜지스터, 메모리, 배선을 생산해 성능과 전력을 향상시키고, 수율 저하 원인인 입자와 결함을 차단할 수 있다.
인텔리전스
고객은 비스타라 플랫폼의 인텔리전스를 통해 제품 출시 기간을 단축하고 양산 과정에서 생산성과 수율을 극대화함으로써 케이던스 및 비용 증가 문제를 해결할 수 있다. 비스타라 플랫폼의 수천 개 센서는 연구 개발부터 공정 이전, 증산, 양산까지 응용되는 어플라이드 AIx 소프트웨어 플랫폼에 방대한 실시간 데이터를 제공한다. 수천 개 공정 변수에서 도출한 실행 가능한 데이터를 통해 엔지니어는 머신러닝과 AI를 활용해 최상의 칩 성능과 전력, 광범위한 공정 윈도우를 구현하는 레시피 생성을 가속화한다.
인텔리전스는 로드락(load lock)의 지능적 제어를 통해 펌프 및 환기 시간을 최적화하는 공장 인터페이스 모듈을 포함한 플랫폼 전반에 통합돼 있다. 이는 반도체 제조사가 입자 및 결함을 줄여 수율 극대화에 도움을 준다.
플랫폼 로봇은 자동 보정으로 작동 개시 시간을 75%까지 줄여준다. 비스타라 플랫폼은 생산 단계에서 자신의 구성 요소를 지속적으로 모니터링하고 보정한다. 이를 통해 수작업을 최소화하고 가동 시간을
극대화하며 유지 보수가 필요한 상황을 예측한다.
지속가능성
반도체 공정의 복잡성과 단계가 늘면 생산에 필요한 에너지와 재료의 양도 증가한다. 비스타라는 2030년까지 등가 에너지 사
용, 화학 물질 사용의 영향 및 클린룸 설치 공간 요구사항을 30% 절감할 수 있도록 설계됐다.
엔지니어들은 비스타라 플랫폼의 가스 패널을 완전 재설계함으로써 등가 에너지 소비량을 종전 제품 대비 50% 이상 절감하고
플랫폼에서 펌프, 열 교환기, 냉각기를 포함한 에너지 집약적 서브팹 컴포넌트 사용 방식을 최적화했다. 이 같은 개선으로 에너
지 소비량을 종전 플랫폼 대비 최대 35%까지 줄여 반도체 제조업체의 스콥1(직접 탄소 배출량)과 스콥2(간접 탄소 배출량) 배
출량 감축에 도움을 준다.
비스타라는 시스템의 클린룸 설치 공간도 최대 30% 절감한다. 고객은 보다 작은 시설에서 동일 양의 웨이퍼를 생산할 수 있다.
2. ‘센튜라 스컬프타(Centura Sculpta)’ 패터닝 시스템
EUV 노광 스텝 줄여 비용 및 복잡성 낮추고
어플라이드 머티어리얼즈가 고성능 트랜지스터 제작 및 배선층 제작 과정에서 EUV 노광 스텝(step)을 줄임으로써 첨단 반도체 제조에 소요되는 비용 및 복잡성을 낮추고, 환경에 미치는 영향을 줄일 수 있는 획기적인 패터닝 기술을 공개했다.
EUV 더블 패터닝 시스템
반도체 제조사는 EUV의 분해능(resolution) 한계보다 작은 반도체 소자를 프린팅할 때 칩 면적 최적화를 위해 EUV 더블 패터닝 사용을 확대하고 있다.
반도체 제조사는 고밀도 패턴을 절반으로 분할하여 프린팅하는 EUV 더블 패터닝을 사용해 EUV의 분해능 한계에 대응하는데, 이때 마스크 2개가 제작되고 절반으로 분할된 패턴은 모두 층간 패터닝 필름에 결합된 후 웨이퍼에 식각된다. 이러한 더블 패터닝은 소자 밀도 증대 측면에서 효과적이지만 설계와 패터닝을 복잡하게 하고 시간, 에너지, 재료, 물이 소비되는 여러 공정 스텝이 필요해 웨이퍼 팹 및 웨이퍼 생산 비용을 높인다.
어플라이드 머티어리얼즈는 추가적인 비용, 복잡성, 에너지, 재료 소비 없이 반도체 제조사가 설계를 축소할 수 있도록 여러 주요 고객사와 긴밀히 협력해 ‘센튜라 스컬프타’ 패터닝 시스템을 개발했다.
반도체 제조사는 싱글 EUV 패턴을 프린팅한 다음 스컬프타 시스템을 사용해 패턴 형태를 원하는 방향으로 길게 늘려 소자 간 간격을 줄이고 패턴 밀도를 높일 수 있다. 최종 패턴은 싱글 마스크로부터 생성되기 때문에 설계 비용과 복잡성이 줄어들고 더블 패터닝 정렬 오류로 인한 수율 저하 위험도 사라진다.
현재 인텔, 삼성전자 등 유수의 반도체 제조사에 각광 받아
EUV 더블 패터닝에는 CVD(화학기상증착) 패터닝 필름 증착, CMP(화학기계연마) 세정, 포토레지스트 증착 및 제거, EUV 노광, 전자빔 계측, 패터닝 필름 식각, 웨이퍼 세정 등 여러 단계의 추가 제조 공정 스텝이 요구된다.
스컬프타 시스템은 EUV 더블 패터닝의 각 시퀀스를 대체하며 반도체 제조사에게 ▲10만 WSPM(Wafer Starts Per Month) 생
산능력당 2억 5,000만 달러 이상의 자본 비용 절감 ▲웨이퍼당 50달러 이상의 생산 비용 절감 ▲웨이퍼당 15kWh 이상의 에너지
절감 ▲웨이퍼당 0.35kg 이상의 이산화탄소에 해당하는 직접 온실가스 배출량 감축 ▲웨이퍼당 15리터 이상의 용수 절감 등의 혜
택을 제공한다.
센튜라 스컬프타 시스템은 현재 인텔, 삼성전자 등 유수의 반도체 제조사 사이에서 각광 받고 있으며, 로직 양산 공정 여러 스텝에서 품질이 검증된 생산 툴로 선택되고 있다.
<저작권자(c)스마트앤컴퍼니. 무단전재-재배포금지>